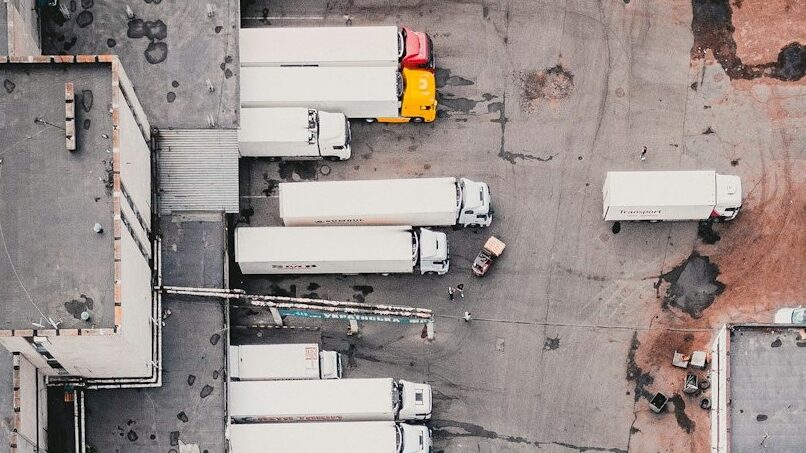
Long Beach, California, is one of the largest and busiest ports in the United States, handling millions of containers each year. For businesses looking to ship freight through Long Beach, understanding the process and addressing common challenges is key to ensuring timely and cost-effective deliveries. In this guide, we’ll explore the freight shipping process in Long Beach, discuss common pain points, and offer practical solutions to help streamline your operations.
The Shipping Process in Long Beach
Shipping freight through Long Beach typically involves the following key steps:
- Booking and Documentation: Choose a shipping carrier and submit the necessary documentation such as bills of lading, commercial invoices, and packing lists.
- Container Loading: Goods are packed into containers at the port or warehouse. Proper packing and labeling ensure safe handling.
- Customs Clearance: For international shipments, goods go through customs inspection and clearance, with necessary tariffs and duties paid.
- Ocean Freight Transit: Goods are shipped by ocean freight to their destination port, with transit times varying based on location.
- Port Arrival and Unloading: Upon arrival, containers are unloaded and go through customs before moving to the next stage of delivery.
- Final Delivery: After customs clearance, goods are delivered to the consignee via trucking or freight forwarding services.
Common Customer Pain Points in Freight Shipping
While shipping freight may seem straightforward, there are common challenges businesses face when shipping through Long Beach. These pain points can cause delays and add unexpected costs:
1. Port Congestion and Delays
Port congestion is a major challenge, with high traffic volumes leading to delays in both loading and unloading containers. This can significantly impact delivery schedules.
Solution: Book shipments well in advance and stay in communication with your carrier or freight forwarder to monitor any potential delays. In some cases, alternative routes or nearby ports may be available.
2. Unpredictable Costs
Freight shipping costs can fluctuate due to factors like fuel prices, seasonal demand, and capacity constraints. Unforeseen price increases can strain budgets.
Solution: Negotiate clear pricing agreements with your shipping provider and plan for possible surcharges. Seek fixed-rate contracts where possible to avoid surprise costs.
3. Customs Compliance Issues
For international shipments, navigating customs regulations can be complex. Mistakes in documentation or classification can cause delays or even fines.
Solution: Work with a customs broker and ensure all documentation is correct and up to date. Stay informed about tariff updates and changes in trade regulations that might affect your shipments.
4. Container Shortages
During busy periods, such as the holiday season or when global supply chains are under pressure, container shortages can be a significant problem.
Solution: Plan shipments early to secure available container space. If containers are scarce, consider using a freight forwarder to help negotiate available space with carriers.
5. Damage to Goods
Shipping long distances and through various handling points exposes goods to the risk of damage, especially if packaging is inadequate.
Solution: Invest in durable packaging materials and work with your shipping provider to ensure goods are properly handled during transit. Consider purchasing insurance to protect against damage or loss.
6. Lack of Visibility and Communication
Freight shipping can sometimes feel like a black box, with businesses not knowing the status of their shipments until they arrive. This lack of visibility can lead to frustration and confusion.
Solution: Choose a carrier or freight forwarder that provides real-time tracking and updates. Use transportation management systems (TMS) or supply chain visibility tools to stay informed throughout the shipping process.
Key Strategies for Success
To overcome the common pain points of shipping freight through Long Beach, consider the following strategies:
1. Work with a Reliable Freight Forwarder
A reputable freight forwarder can help streamline your shipping process, offering expertise in handling logistics and paperwork, and ensuring timely deliveries. They can also advise on cost-saving routes.
2. Diversify Shipping Routes and Ports
To avoid delays caused by port congestion at Long Beach, consider diversifying your shipping routes and exploring other nearby ports like Los Angeles or Oakland.
3. Invest in Technology
Technology can help improve visibility and efficiency. Use transportation management systems (TMS) or supply chain visibility tools to gain real-time updates on shipments.
4. Plan Ahead for Peak Seasons
During peak seasons, shipping demand surges. Book shipments early to ensure space and avoid delays caused by high demand.
Conclusion
Shipping freight through Long Beach can be efficient and cost-effective, but it comes with its set of challenges. By understanding the common pain points such as port congestion, unpredictable costs, and customs issues, businesses can better prepare and streamline their shipping process. By leveraging technology, working with reliable partners, and planning ahead, businesses can ensure that their freight shipping experience is smooth, cost-effective, and timely.